Company Name | Contact Info | Location | ||||||||||||
---|---|---|---|---|---|---|---|---|---|---|---|---|---|---|
KENSAN MAKİNA SANAYİİ VE TİCARET LTD. ŞTİ.
SARAY MAHALLESİ 66. CADDE NO: 8 / KAHRAMANKAZAN / ANKARA / TÜRKİYE
|
Contact Info: +90 312 385 8841
|
Hall: 1
Stand: 100
|
||||||||||||
Product Groups | ||||||||||||||
|
- Company Info
- Products
- Represented Companies
- Company Brands
Our company has been manufacturing stone crushing, screening and washing machines for mines since its inception. Our company, which adopted the honest work and making high-quality reliable machines as principles, is advancing rapidly by being loyal to total quality understanding, doing continuous research and development in its sector and complying with quality standards to become an important and outstanding name in its sector. Our company makes all its activities professionally, works with all energy during and after the service in order not to disappoint you. Complete facilities (plants) we manufacturing Fixed crushing and screening plant Mobile crushing and screening plant Mechanical stabilization facility (plant) Portable washing and screening facility (plant) Fixed washing and screening facility (plant) Fixed screening storage facility Gravel washing Mobile primary crushers
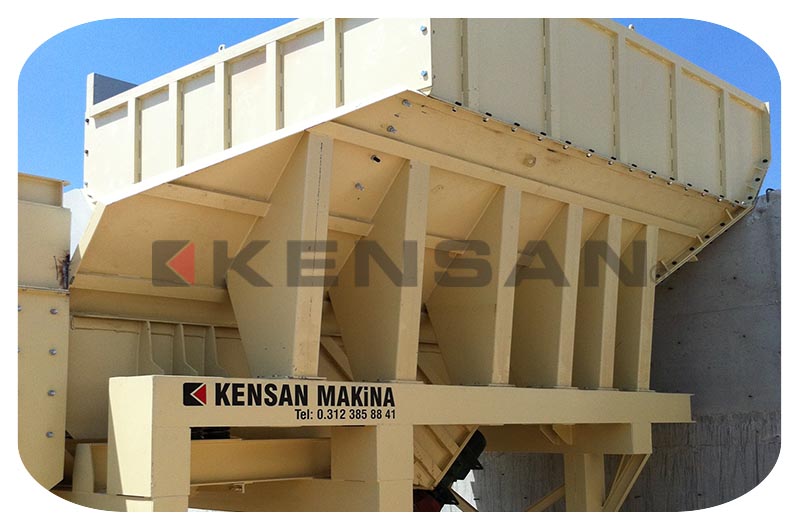
These are the feeders driven by two each robust-type vibromotors working synchronized with each other supported by the heavy - duty type helical springs ensuring regular transmission of the raw material coming from the quarry to the primary crushers. Thanks to the manganese grids found at its front section, the clearance sizes of which can be adjusted, the earthy substances in the raw material are thrown out of the system before it enters the primary machine. In parallel to the request, the materials that come out hereof can be re-sieved with a suitable sieve and any material escaped during such discharge can be re-included into the system. Feeding capacity in the vibratory feeders we manufacture with the vibromotor oscillating feeders we have manufactured can be adjusted. In this way, the primary machine is fed regularly and the feeders are not exposed to be activated / paused constantly.
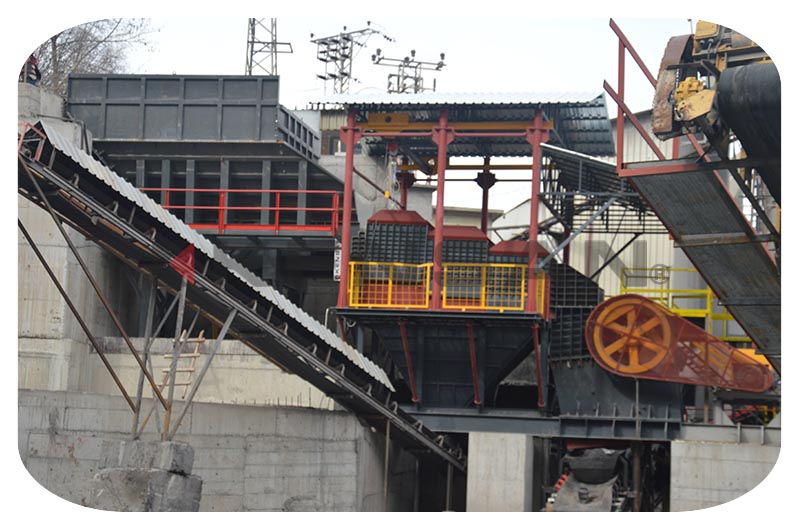
The biggest problem of the mines and quarries, blockages occurring on vibration feeders and grid screens due to wet, sludgy and sticky materials, can be solved by wobbler feeder. Thanks to the dredges under the self-cleaning discs, the fine materials, clods and waste materials, not desired to be fed to the main breaker, are discharged without penetrating into the main breaker throughout the clearance determined in the design and a clean feeding and a regular feeding rate are ensured.
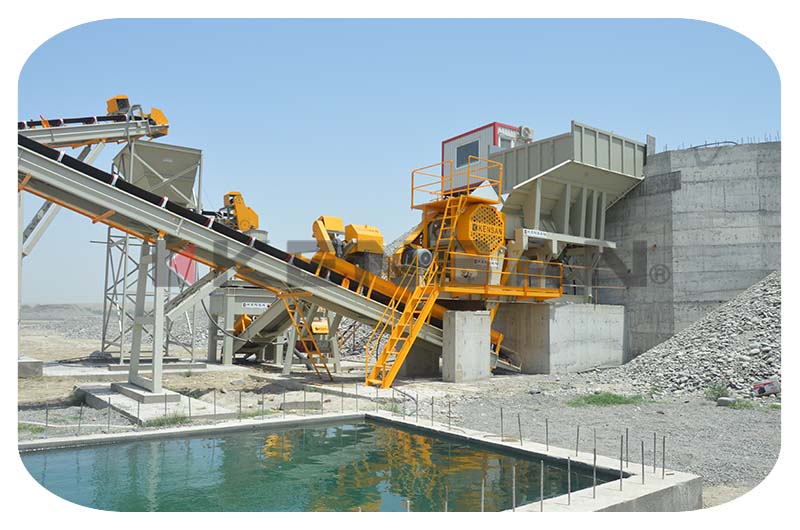
Primer ve sekonder olarak kullanılan bu kırıcılar mohs sertliği yüksek ( dere ve bazalt) malzemeleri kırmak için ideal kırıcılardır. Sabit ve hareketli iki adet çene ile malzemeyi sıkıştırarak kırar. Makinaya giren malzeme kırılamayacak kadar sert ise çeneli kırıcılar belli bir yükte kırılan emniyet plakaları sayesinde kendisine zarar vermez. Ana gövde gerilime ve yüksek basınca dayanıklı sacdan imal edilmektedir. Malzemenin kırılırken temas ettiği çeneler ve yan astarlar %16-18 mangan %1,5 molibden alaşımlı çelikten döküm olarak imal edilmektedir. KENSAN Çeneli Kırıcılarda hassas işlemeli, ısıl işlemden geçirilmiş SAE 4140 çelik eksantrik mil kullanılmaktadır. Pitman milindeki eksantriklik değerinin yüksek olması sayesinde malzemenin çenenin altına doğru hareket etmesini sağlayan bir hareket kazandırılmıştır.
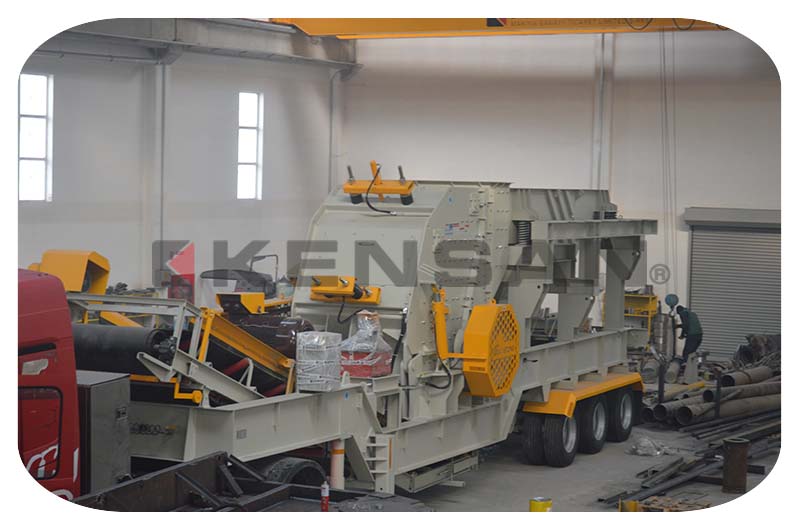
The Primary Impact Crushers make the less abrasive materials of medium hardness smaller with a high ratio. The materials from the quarry are processed with the primary impact crushers firstly. They have the ability to crush the materials up to 1 meter x 1 meter size to a size of 25 mm. There are 2 pieces of manganese coated adjustable crushing chamber. All surfaces that come into contact with broken stone covered with manganese undercoats. Crushing process is done with the 4 palettes of high-alloy manganese in a rotor weighing 8500 kg and rotating with 450 revolutions per minute.
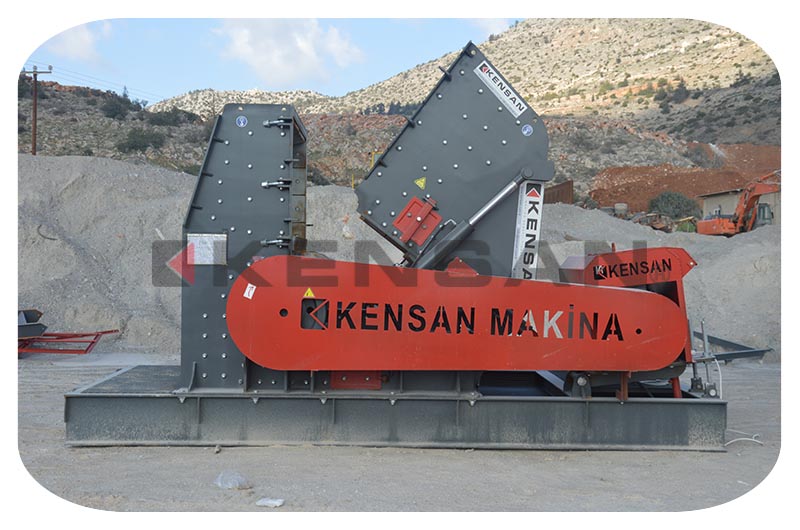
The DMK series of jaw crushers counted as the impact crushers with adjustable jaws are the crushers which can break the materials with middle and high hardness (such as limestone, dolomite, granite and basalt).To be fed with coarse material, cubic product acquisition, having a high reduction ratio, ability to work at high capacity, low investment and operating costs, has made this type of breakers an ideal secondary crusher in crushing and screening facilities The stone put into the crusher, crash to the crushing elements of the first region through the throw of rotor hammers, and a first crushing step takes place. In this region consist a high pressure and crushing power which can even break very hard materials. The desired sizes of the broken material pass through the second region. The material in second area passes through another crushing stage and reduced to smaller dimensions. Then, the material passes through the third and final area and crushing process takes place the last time. Now the material is reduced to the smallest sizes (which the machine is able to crush). Secondary Impact Crusher
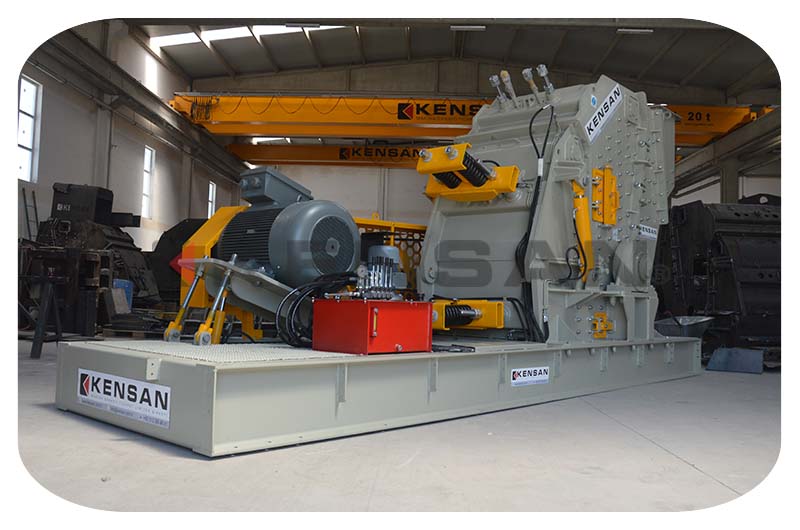
PSK series crushers, which are jaw-adjusted impact crushers, are crushers that break medium and high hardness materials (such as limestone, dolomite, granite and basalt) in the size of asphalt and concrete aggregate. Coarse material feeding, cubic product, high reduction ratio, high capacity, low investment and operating cost have made this type of crusher the ideal secondary crusher in crushing and screening plants. The stone entering the crusher hits the crushing elements in the first region with the swing of the rotor hammers and the first crushing stage takes place. In this region, high pressure and breaking power are created to break even very hard materials. If the crushed material is in the desired dimensions, it passes to the second zone. The material passing to the second zone passes through another crushing stage and is reduced to smaller sizes. Then the material passes to the third and last zone and the final crushing process takes place. Now the material is reduced to the smallest dimensions.
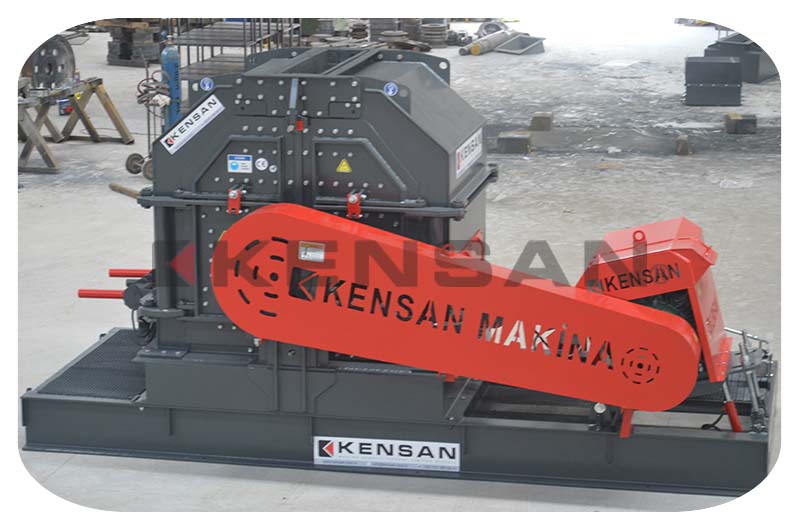
Tertiary Impact Crushers are high-speed machines that are used to obtain sand. The material entered into the machine, exits the machine after that it is hit against the walls and crushed by a high-speed (800 r / min) rotor. The material generally left over the screen is broken in these crushers, which usually are used to obtain 0-5 mm sand.
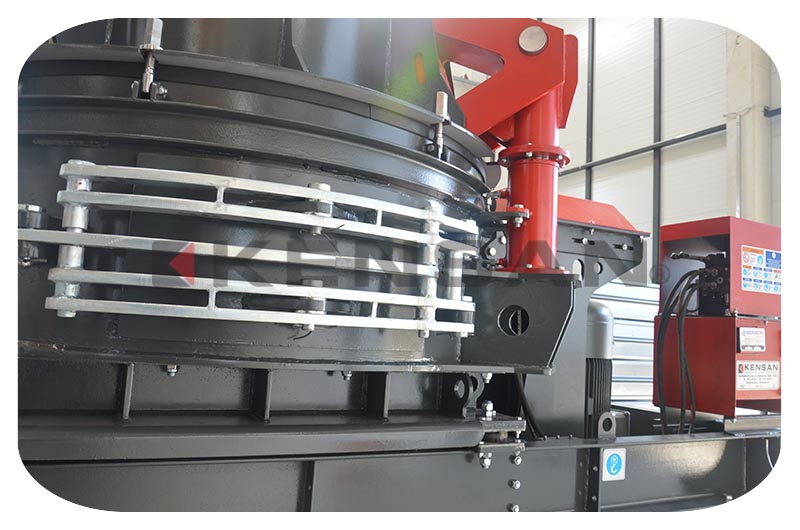
VSI crushers are the tertiary type of crushers used to crash the hard and abrasive materials between 0-45 mm, bring them into cubic shape and obtain sand. VSI crushers are produced in two types as closed rotor and open rotor. The vertical shaft types of crushers with closed rotor are fed with stones maximum size of 0-45 mm. because some large material in return of the crashed material can leave on the screen; these types of crushers are not suitable for crashing the returned material. VSI crushers shoot and crush the material, which entered into the rotor, by throwing them to the lining of stones stone box which formed in the stator naturally and to the materials which entered in the system from the outside of the rotor with a speed of 67 - 80 m / s approximately (crushing stones by hitting stones). VSI crushers are used to crush the materials having hardness lower than the grade 9 with a moisture content of less than 9%. Non-flammable and non-explosive mining materials have to be used.
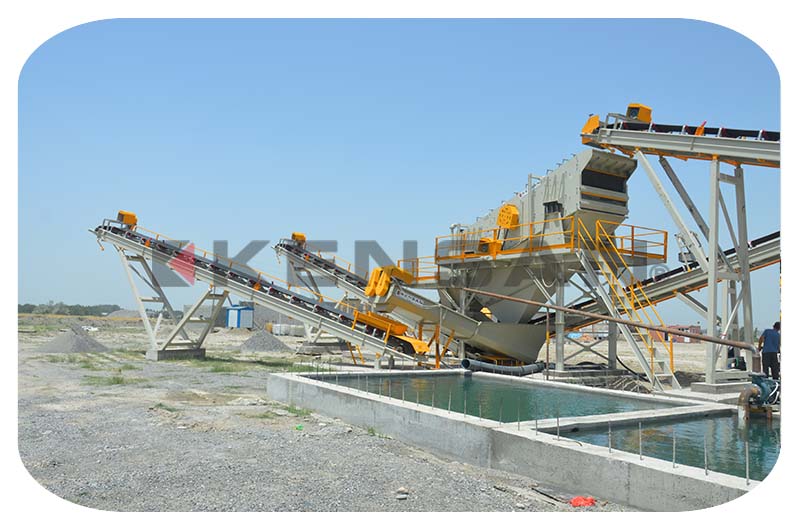
Vibrating sieves are theoretically manufactured in every possible size with 1,2,3,4 layers. They are used in the dimensioning process of the material broken by the crushers. The capacity of the sieve changes according to the desired product size. The free vibrating screens operate at an average amplitude of 7 mm. The gradation and moisture of the material to be sieved plays an important role in the capacity of the sieve. The vibration-resistant special bearings and the shaft housed in the sieve body are driven by the oscillation-adjustable weights installed at both ends of the shaft. There is an ellipsoidal vibration in the back and front sections and circular vibration in the center of the sieve. The vibration body sits on the main chassis with a sufficient number of heavy-duty helical springs. The inter-layers spacing has been designed rather wide in all KENSAN sieves. The front chute has been designed to be a sliding system so that the service element can easily enter between the layers when necessary. Thus, the time to replace the sieve wires is shortened. This feature significantly decreases the downtime and service time of the machine.

Belt Conveyor is major transmission element of mining facilities. They are manufactured in various widths and lengths according to the capacity and distance will be transmitted. The belt conveyors can be manufactured in width of 400-500-600-650-750-800-1000-1200-1400 mm and in desired length. They are driven by belt-pulley-reducer or by engine and reducer coupled directly.
No represented companies found.
- KENSAN MAKİNA